Un desarrollo del LEMaC Centro de Investigaciones Viales -dependiente de la UTN Facultad Regional La Plata y de la Comisión de Investigaciones Científicas- fue premiado en el concurso INNOVAR, del Ministerio de Ciencia, Tecnología e Innovación de la Nación, en la categoría de “Desarrollo Sustentable y Energía”.
Se trata de la creación de la “Piedra-Polimérica para uso vial”, un agregado de trituración hecho a base de residuos plásticos domiciliarios y suelos finos, que se puede aplicar en capas de pavimentación en reemplazo del recurso natural, que es la piedra partida que se extrae, por ejemplo, en Olavarría.
No es el primer reconocimiento que le llega a este proyecto: en mayo ya había recibido otro galardón, en este caso internacional, en un concurso realizado en Italia. Fue premiado con un “Iron A’ Design Award” en la categoría “Circular Economy and Waste Reduction Design 2022-2023” (Economía Circular y Diseño de Reducción de Residuos).
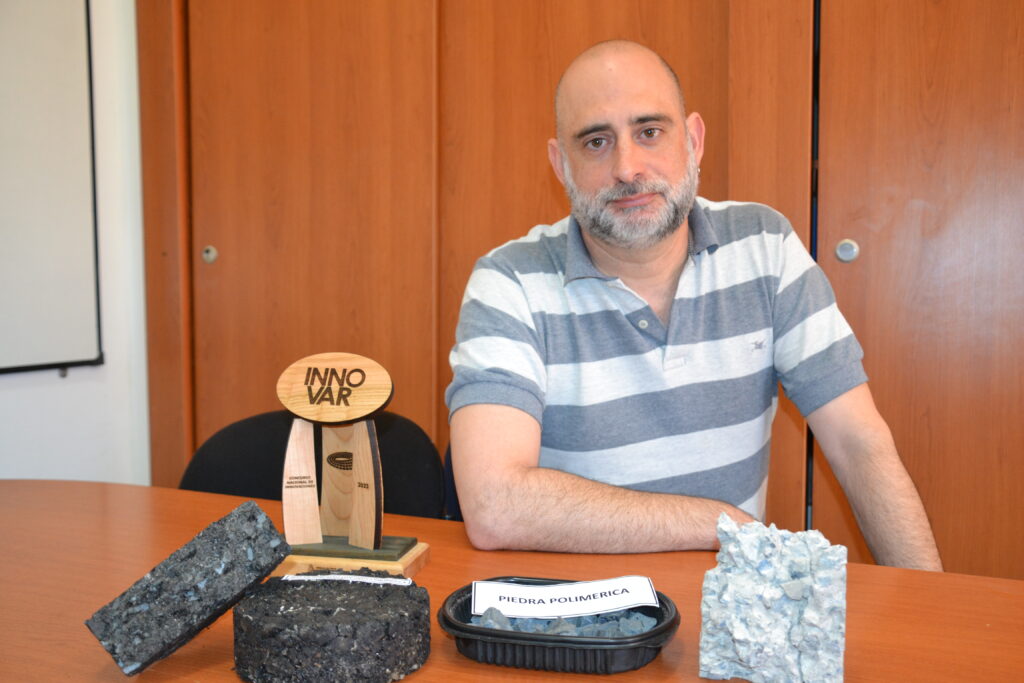
La aplicación de este desarrollo tiene el potencial de influir directamente tanto en los costos de la pavimentación como en el impacto ambiental que genera el uso de plásticos; y además podría ser un generador de mano de obra a escala local.
“Con esto podemos aportar a la solución de los problemas ambientales de explotación de la piedra en origen y su transporte, y a la disminución del pasivo ambiental del plástico de residuos domiciliarios. También podemos generar empleo en cooperativas que vean de mejor modo el tema de separación o en pymes que se interesen en desarrollarla, facilitando el incremento de mano de obra local. De ese modo, obtenemos un agregado con menor costo; que implicaría a nivel municipal pavimentar más kilómetros con el mismo dinero”, explicó Julián Rivera, director del LEMaC.
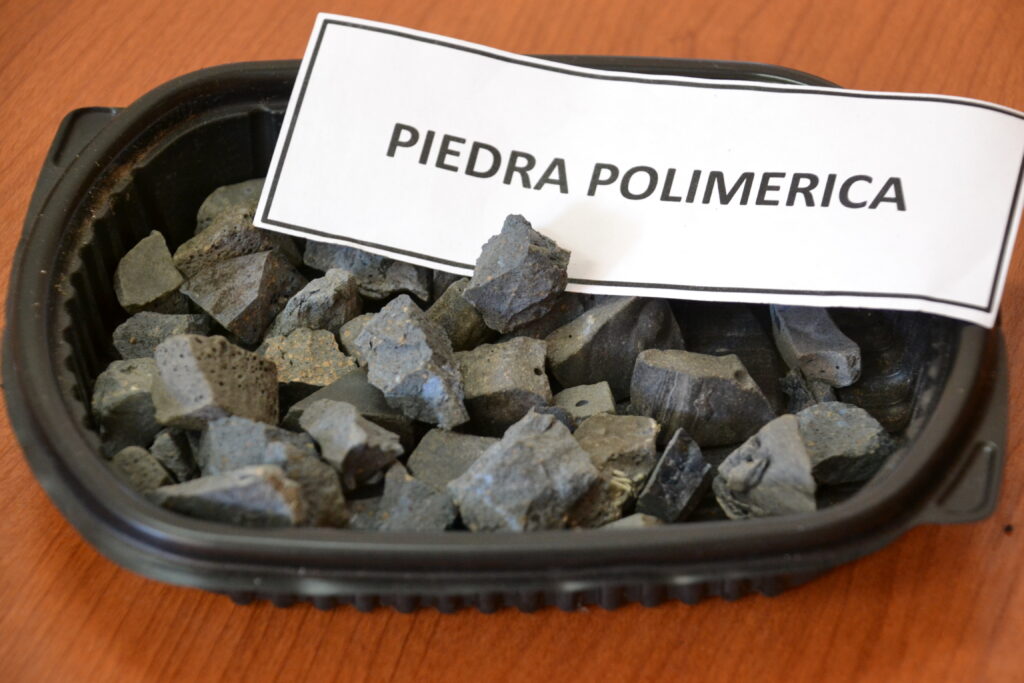
El proceso de producción
Dentro de lo que se denominan residuos poliméricos domiciliarios -que son los plásticos- en el LEMaC han tomado de ejemplo el polipropileno, que es el que se utiliza para algunos materiales textiles (barbijos, friselina) o también envases, vasos, bandejas y tapitas de gaseosa, entre otros productos.
“Si bien podríamos usar distintos plásticos, nuestras experiencias se basan en el empleo de polipropileno, aunque con conclusiones extrapolables a toda una serie de polímeros similares por separado. Lo que no podemos es mezclar esos polímeros, porque tienen distintas temperaturas de fusión”, explicó el ingeniero e investigador.
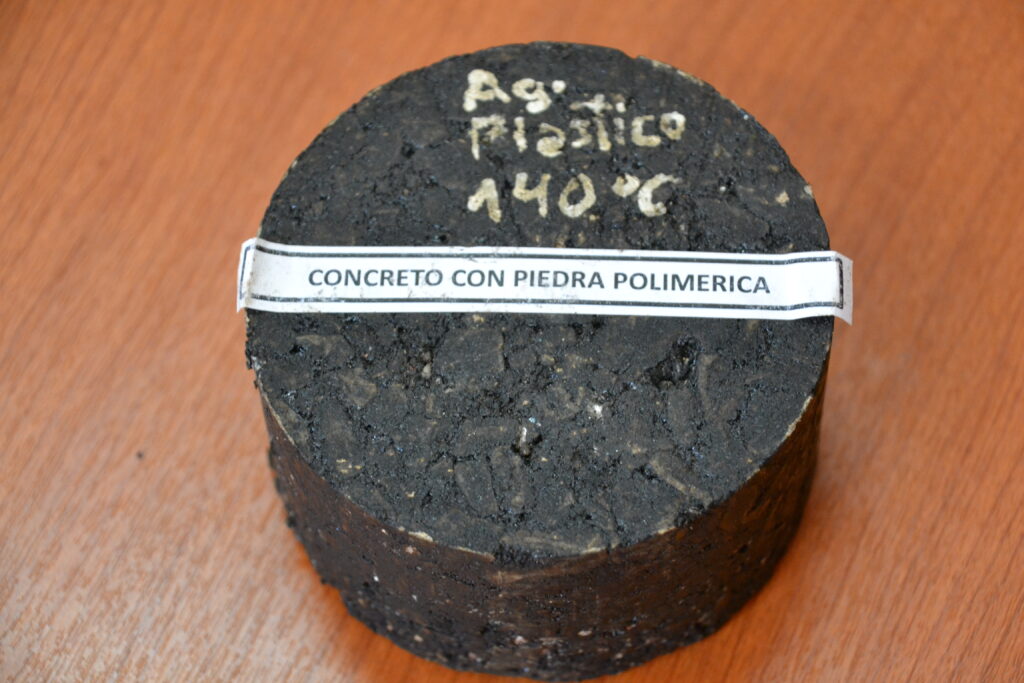
El proceso de producción, que está en vías de ser patentado por el LEMaC, implica llevar “el polipropileno a su temperatura de fusión, aproximadamente 170 ºC, mezclarlo con el suelo y generar piezas que solidifican a temperatura ambiente. Esas piezas luego se trituran, dando lugar a la piedra partida, que es la que utilizamos nosotros, con tamaños por debajo de los 20 milímetros”.
Según detalló Rivera, el resultado es una piedra que comparada con la versión “natural” tiene apenas “alguna diferencia de peso, pero que cumple con los requisitos de una piedra de uso vial. Lo que proponemos es utilizarla en vías de bajo volumen de tránsito, que sería la pavimentación de calles suburbanas o caminos rurales. No es para usarlo en algo de alta categoría”.
La piedra partida se suele utilizar en las capas de base en pavimentación, como constituyente de estabilizados granulométricos. “Si no es con contenidos de cemento y muy buen suelo, lo habitual es que la base de un pavimento sea una mezcla de piedra, arena y suelos, ahí podría entrar esta piedra. Además, puede utilizarse en la capa de rodamiento, o sea la capa superior del pavimento, constituyendo la mezcla asfáltica. En este caso se hace en frío, porque la piedra no aguantaría la alta temperatura en la elaboración de la mezcla en caliente. La idea es que entre mayoritariamente ahí, en la capa de rodamiento asfáltica, pero se puede usar también en la base”, remarcó.
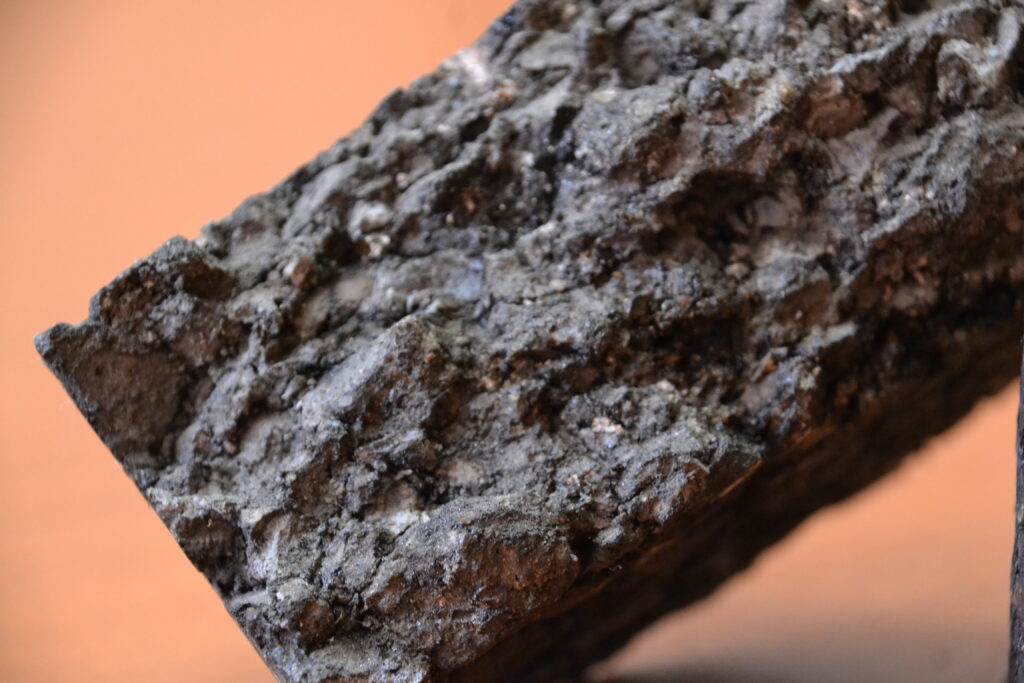
El proyecto permitiría disminuir los costos del transporte, que según calculan en el LEMaC pueden alcanzar el 80% del precio final del agregado, teniendo en cuenta que la piedra partida se traslada desde Olavarría hacia distintos puntos de la Provincia. Pero, además, impacta directamente en el problema ambiental que implica por un lado la extracción de piedra en origen y por otro la producción de residuos plásticos domiciliarios.
Según datos del CEAMSE, la empresa pública que realiza la gestión integral de los residuos sólidos urbanos del AMBA, los plásticos representan el segundo grupo en magnitud que recibe (18,82 %) detrás de los materiales orgánicos. La producción de esta piedra permitiría reciclar un porcentaje de éstos.
“Para escala local andaría muy bien. Porque no es una tecnología del otro mundo. A nosotros como Universidad nos interesa mucho. Si bien lo estamos patentando, sería una oportunidad de extensionismo de una universidad pública. Podemos brindar asesoramiento, hacer la aplicación y generar producción de esta piedra”, afirmó Rivera.
Por David Barresi